

Aluminum
Why alumínio?
Products
Discover our complete line of primary and processed products:

Primary products
They are used in the manufacture of cables and wires and in the foundry, rolling and deoxidation industries.
Veja mais detalhes sobre as especificações dos produtos primários da CBA.

Processed products
Used in the transport, automotive, construction, energy, packaging and consumer goods industries.
Veja mais detalhes sobre as especificações dos produtos transformados da CBA.
Learn more about our production process
Applications
Did you know?
CBA produces aluminium products that are used across all three segments of the electricity supply chain: generation, transmission and distribution.

Generation
In generation, we provide solutions for photovoltaic panels, aluminum roofing structures for floating plants, and aluminum for large hydroelectric dam structures.

Transmission
In transmission, we supply sheet and foil to transformer manufacturers.

Distribution
In distribution, we supply aluminum profiles used to make conductor tubes for substations.
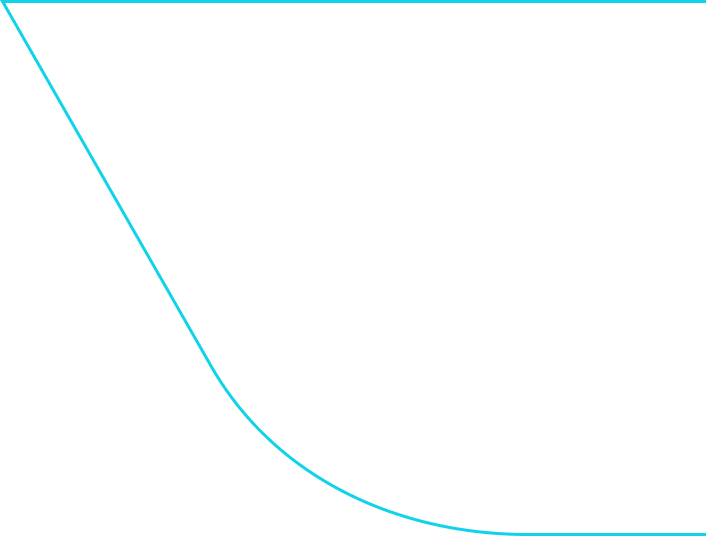
Innovation and market development
We recognize that a better future can only be built by working together. That is why we develop co-creation and co-engineering projects that leverage our delivery of solutions and create and share value from our projects.
This provides opportunities to deploy new technologies and new business models, and strengthens our long-term relationships.

Innovation Manifesto
At CBA we believe that each of us can INNOVATE!
Innovation is a part of our history. For more than six decades, we have delivered products, services and solutions that have helped to shape society, driving transformations beyond our industry.
We believe transparency and employee engagement with the external environment, combined with a trust-based working environment that is open to new ideas, can catalyze innovation. In this journey, we give employees autonomy to experiment and gain new experience, and we implement initiatives and methodologies that encourage intra-entrepreneurship, in line with our values of product safety and quality.
Solutions and services
CBA has two Solutions & Services Centers (CSS), one at our plant in Alumínio (SP) and the other at our facility in Caxias do Sul (RS).
These centers cater to customers’ aluminum processing needs within co-engineering projects, such as grit blasting, anodizing, coating, special cutting operations, machining and market-ready kit assembly.
Some of our ongoing project-related services include:
Co-engineered solutions
CBA has pioneered the development of co-designed and co-engineered automotive solutions and structural components.
Examples of these solutions include aluminum door protection bars and bumpers that increase vehicle safety. The high-strength extruded aluminum used to make these parts offers geometric flexibility and avoids the high tooling costs involved in producing stamped steel parts.
Co-engineered solutions are expanding CBA’s portfolio of high-strength alloys for structural applications, previously only available in other markets.